Plastic extrusion for robust and easy-to-handle components
Plastic extrusion for robust and easy-to-handle components
Blog Article
Key Benefits and Factors To Consider of Implementing Plastic Extrusion in Your Projects
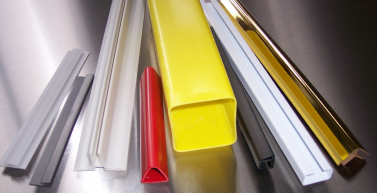
Understanding the Fundamentals of Plastic Extrusion
Plastic extrusion, a staple in the production market, is a procedure that includes melting raw plastic material and improving it right into a continual account. This account, once cooled down, can be cut into desired sizes or curled for later usage. The charm of plastic extrusion lies in its adaptability. A large range of items, from piping to window frameworks, can be produced. The process calls for an extruder, a detailed device with a heated barrel, a rotating screw, and a die at the end. The plastic material, in the kind of pellets, is fed into the extruder, where it's thawed and compelled with the die, taking its shape. The selection of plastic and the layout of the die figure out the product's features.
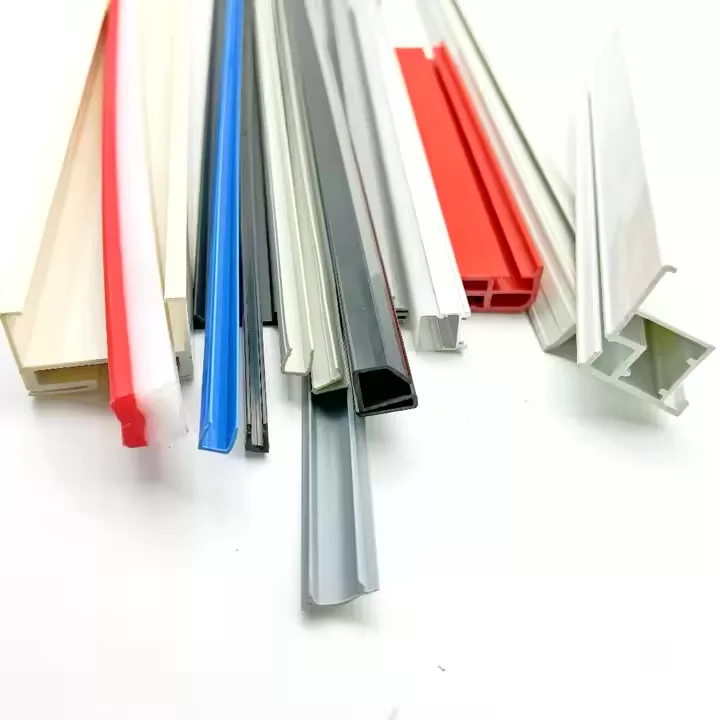
The Economic Advantage of Plastic Extrusion
The financial advantage of plastic extrusion exists mostly in two locations: economical material manufacturing and valuable production rates. With plastic extrusion, companies can produce high volumes of material at a lower expense compared to various other techniques. The process flaunts a remarkable manufacturing rate, substantially lowering time and additional enhancing its economic viability.
Cost-efficient Material Production
A significant benefit of plastic extrusion is its amazing cost-effectiveness. This manufacturing procedure enables constant, high-volume manufacturing with very little waste, which translates into reduced costs. The raw products made use of, usually plastic pellets, are relatively low-cost compared to other compounds (plastic extrusion). The procedure itself needs less power than lots of other production approaches, better reducing prices. In addition, the extrusion procedure permits a high level of precision in shaping the plastic, reducing the need for pricey post-production changes or improvements. In addition, the sturdiness and longevity of extruded plastic products usually suggest much less need for substitutes, adding to long-term savings. All these elements make plastic extrusion a highly affordable choice for many jobs, providing an appealing equilibrium in between cost and performance.
Beneficial Manufacturing Speeds
While keeping the cost-effectiveness of the materials, one more significant benefit of plastic extrusion exists in its quick manufacturing rates. This performance in the production process is associated to the constant nature of the extrusion procedure, enabling high-volume manufacturing in a reasonably short time span. The rate of production straight associates to a decline in labor expenses and a rise in result, thus improving the general financial feasibility of the procedure. In addition, the busy production does not jeopardize the top quality of More Help the end product, guaranteeing dependable and consistent results. This combination of quality, rate, and cost-effectiveness highlights the significant economic benefit of applying plastic extrusion in various jobs.
Flexibility and Modification: The Staminas of Plastic Extrusion
One of the famous strengths of plastic extrusion lies in its versatility and modification capacity. These qualities unlock to unlimited layout opportunities, offering producers the ability to tailor products to details requirements. This increased degree of customization not just enhances product performance but likewise considerably enhances product individuality.
Unrestricted Layout Opportunities
Plastic extrusion shines in its capability to offer nearly unlimited layout possibilities. Plastic extrusion can manage a selection of plastic types, broadening its application scope. With plastic extrusion, the style possibilities are essentially endless.
Enhancing Product Uniqueness
The convenience of plastic extrusion can greatly enhance product individuality. This procedure allows designers to experiment with various shapes, sizes, and colors, providing the flexibility to produce special products that stand out in the market. It is this customization that offers a distinctive identification per web product, distinguishing it from its rivals.
Along with its aesthetic benefits, the customizability of plastic extrusion also offers sensible advantages. Designers can modify the properties of the plastic according to the details demands of the application, boosting the product's functionality. As an example, they can make the plastic extra versatile, much more sturdy, or a lot more immune to warmth, relying on what the item calls for. Hence, plastic extrusion not only improves product individuality but additionally its utility and marketability.
Layout Limitations in Plastic Extrusion: What You Required to Know
Just how can design restrictions potentially impact the process of plastic extrusion? While plastic extrusion is flexible, style constraints can stop its benefits. Understanding these constraints is essential for effective implementation of plastic extrusion in your projects.
Assessing the Environmental Impact of Plastic Extrusion
While recognizing layout constraints is a substantial facet of plastic extrusion, it is just as essential to consider its environmental implications. The process of plastic extrusion involves melting plastic products, possibly launching unsafe gases right into the environment. Additionally, the resulting items are commonly non-biodegradable, adding to land fill waste. However, innovations in modern technology have actually permitted even more environmentally-friendly methods. Using recycled plastic products in the extrusion process can lower ecological impact. Furthermore, creating eco-friendly plastic choices can assist minimize waste issues. Reviewing these ecological elements is crucial when carrying out plastic extrusion projects, guaranteeing an equilibrium in between efficiency, cost-effectiveness, and ecological obligation.
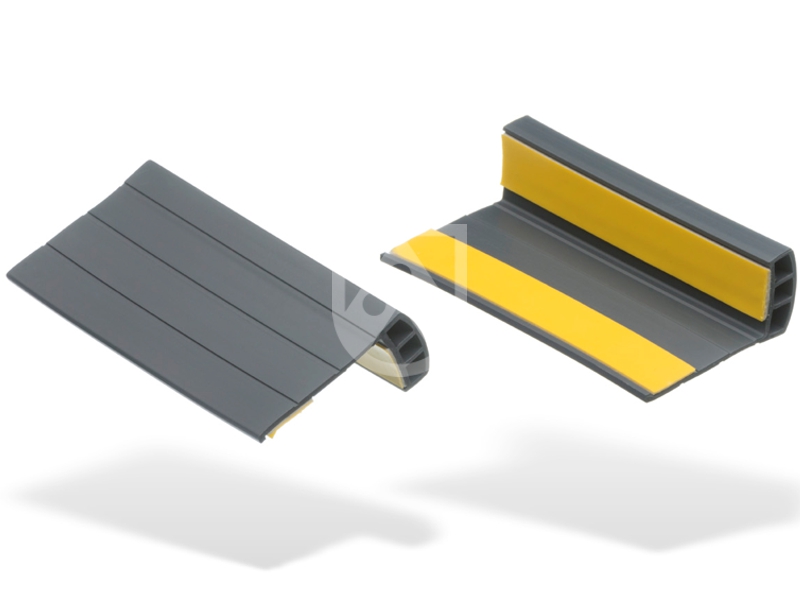
Study: Effective Projects Making Use Of Plastic Extrusion
Success stories in the area of plastic extrusion are plentiful, showing both the flexibility and efficiency of this production procedure. One notable example is the production of PVC pipelines made use of in modern-day plumbing. This procedure involves melting plastic and creating it into a continual tube, offering significant cost and toughness benefits. An additional effective instance is the manufacturing of plastic movie for product packaging and agriculture. With extrusion, makers can create highly personalized, slim, and durable movies. Automotive sectors additionally profit, utilizing extruded plastic for components like trim or seals, boosting lorry longevity. These circumstances illustrate plastic extrusion's critical find out function in numerous markets, proving to its adaptability, cost-effectiveness, and reputable outcome.
Final thought
In final thought, plastic extrusion uses a affordable and effective technique for producing intricate forms with minimal waste. Integrating plastic extrusion into jobs can lead to successful end results, as evidenced by numerous situation researches.
Plastic extrusion, a staple in the production industry, is a process that involves melting raw plastic material and improving it into a continual profile. Plastic extrusion can deal with a variety of plastic types, expanding its application scope.How can make constraints potentially affect the procedure of plastic extrusion? The process of plastic extrusion involves melting plastic materials, potentially releasing unsafe gases right into the setting. Making use of recycled plastic products in the extrusion procedure can lower ecological effect.
Report this page